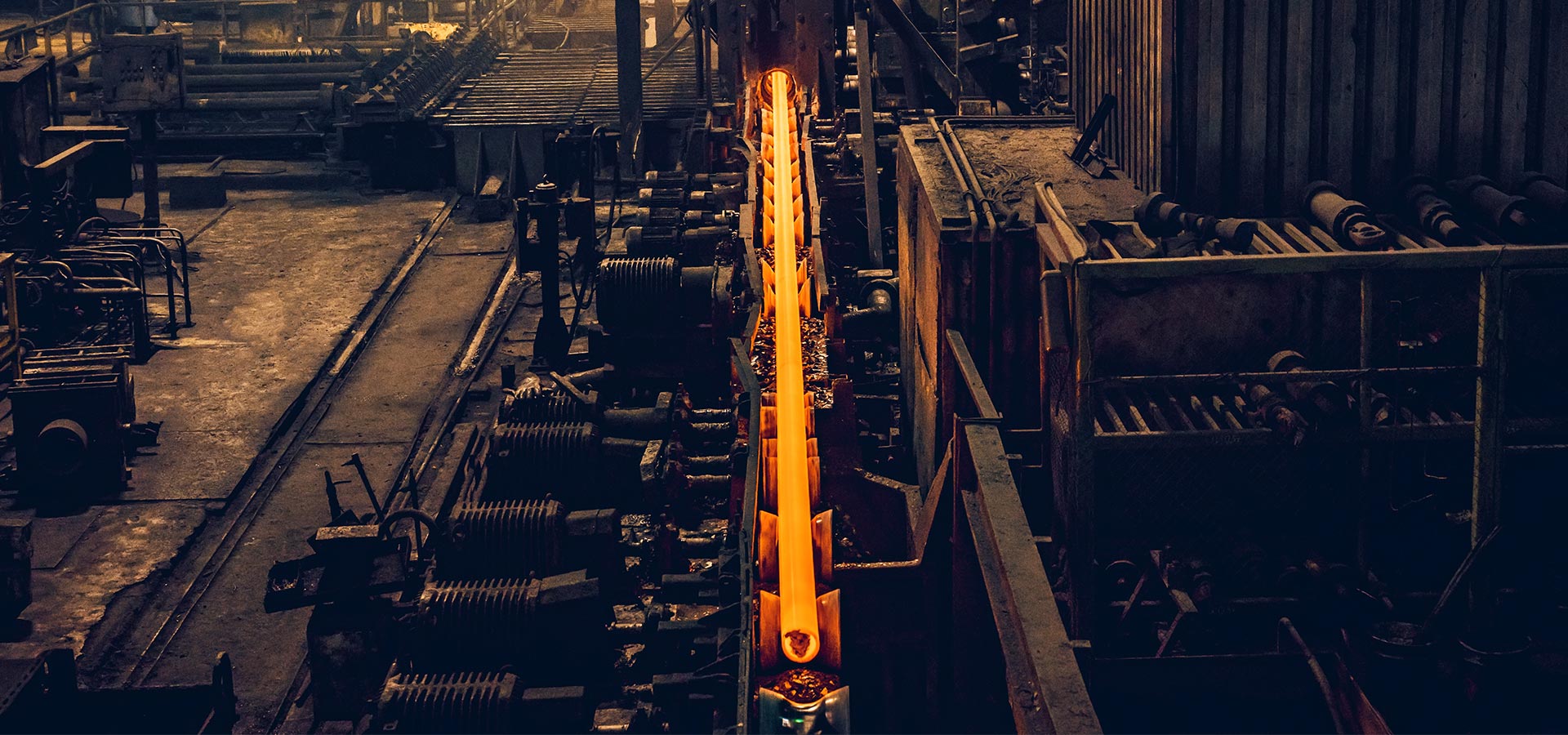
Introduction
In the world of piping, two prominent types stand out: seamless and Electric Resistance Welded (ERW) pipes. Each type has its own unique characteristics, advantages, and applications. This guide will delve deep into the differences between seamless pipes and ERW pipes, providing you with the insights needed to make informed decisions for your projects. Whether you’re in construction, oil and gas, or manufacturing, understanding these differences is crucial.
What is Seamless Pipe?
Seamless pipes are produced without any welding or seam. They are made by extruding a solid billet through a die to create a hollow tube. This process results in a pipe with a uniform structure and superior strength. Seamless pipes are known for their high pressure and high-temperature resistance, making them ideal for critical applications.
Manufacturing Process of Seamless Pipes
- Billet Heating: A solid steel billet is heated to a high temperature.
- Piercing: The heated billet is pierced to create a hollow tube.
- Elongation: The hollow tube is elongated and rolled to the desired dimensions.
- Finishing: The pipe undergoes various finishing processes such as sizing, straightening, and heat treatment.
Advantages of Seamless Pipes
- Superior Strength: No seam means no weak points, providing higher strength.
- High Pressure and Temperature Resistance: Suitable for extreme conditions.
- Uniform Structure: Ensures consistent performance.
What is ERW Pipe?
Electric Resistance Welded (ERW) pipes are fabricated by rolling metal and then welding it longitudinally across its length. The welding process is done by applying pressure and passing an electric current through the metal, which heats and fuses the edges together.
Manufacturing Process of ERW Pipes
- Coil Preparation: Steel coils are cut to the required length.
- Forming: The cut steel is formed into a cylindrical shape.
- Welding: The edges are welded using electric resistance welding.
- Sizing and Shaping: The welded pipe is sized and shaped to the desired dimensions.
- Heat Treatment: The pipe is heat-treated to remove any residual stress.
Advantages of ERW Pipes
- Cost-Effective: Generally cheaper than seamless pipes.
- Consistent Dimensions: The welding process ensures uniformity.
- High Production Efficiency: Suitable for mass production.
Key Differences Between Seamless and ERW Pipes
Understanding the key differences between seamless and ERW pipes is essential for selecting the right type for your application. Here’s a detailed comparison:
Aspect | Seamless Pipe | ERW Pipe |
---|---|---|
Manufacturing | Extruded from a solid billet | Formed and welded from a steel coil |
Strength | Higher due to lack of seam | Slightly lower, but sufficient for many uses |
Pressure Rating | Can handle higher pressure | Suitable for moderate pressure applications |
Temperature | Suitable for high-temperature environments | Generally used in lower temperature environments |
Cost | More expensive due to complex manufacturing | More cost-effective |
Applications | Oil and gas, power generation, high-pressure systems | Water pipelines, structural applications, automotive |
Uniformity | Consistent structure throughout | Consistent dimensions but with a welded seam |
Applications of Seamless and ERW Pipes
Both seamless and ERW pipes have their specific applications based on their properties:
Applications of Seamless Pipes
- Oil and Gas Industry: Used in drilling and transportation due to their high pressure and temperature resistance.
- Power Generation: Ideal for transporting steam and other high-temperature fluids.
- Chemical Processing: Suitable for handling corrosive and high-pressure substances.
- Automotive: Used in high-stress components like fuel injection systems.
Applications of ERW Pipes
- Water Pipelines: Commonly used for transporting water due to their cost-effectiveness.
- Structural Applications: Used in construction for scaffolding, columns, and beams.
- Automotive Industry: Suitable for exhaust systems and other low-pressure applications.
- Agricultural Equipment: Used in various types of machinery and equipment.
Selecting the Right Pipe for Your Application
Choosing between seamless and ERW pipes depends on several factors, including the specific requirements of your project. Here are some considerations:
1. Pressure and Temperature Requirements
- High Pressure/Temperature: Seamless pipes are the better choice.
- Moderate Pressure/Temperature: ERW pipes can be used effectively.
2. Cost Constraints
- Budget-Friendly: ERW pipes are generally more economical.
- High-Performance Needed: Seamless pipes, though costlier, provide superior performance.
3. Application Specifics
- Critical Applications: Seamless pipes are preferred for their reliability.
- Non-Critical Applications: ERW pipes can be used to save costs.
4. Availability
- Mass Production: ERW pipes are widely available and can be produced in large quantities.
- Specialty Uses: Seamless pipes might be more difficult to source but are necessary for specialized applications.
Detailed Analysis of Strength and Weaknesses
Strength of Seamless Pipes
Seamless pipes are known for their exceptional strength due to the absence of a seam. This makes them ideal for high-stress environments where pressure and temperature can fluctuate significantly. The uniformity in the structure of seamless pipes also means they are less likely to fail under pressure, reducing the risk of leaks or bursts.
Weaknesses of Seamless Pipes
The main drawback of seamless pipes is their cost. The complex manufacturing process involves higher material and labor costs, making seamless pipes more expensive than ERW pipes. Additionally, the production of seamless pipes is less efficient, leading to longer lead times and potential availability issues.
Strength of ERW Pipes
ERW pipes are highly valued for their cost-effectiveness. The manufacturing process is straightforward and efficient, allowing for mass production at a lower cost. The welding process ensures consistent dimensions, which is crucial for applications requiring precise measurements.
Weaknesses of ERW Pipes
While ERW pipes are generally strong, the presence of a seam makes them more vulnerable to failure under extreme pressure and temperature conditions. The welded seam can be a weak point, particularly in applications where the pipe is subjected to high stress. Additionally, ERW pipes are not suitable for high-temperature environments, limiting their use in certain industries.
Impact of Material Selection
The material used in manufacturing both seamless and ERW pipes plays a significant role in determining their performance. Common materials include carbon steel, alloy steel, and stainless steel, each with its own set of properties.
Carbon Steel
Carbon steel is widely used due to its strength and affordability. It’s suitable for a range of applications, but it can be prone to corrosion if not properly treated.
Alloy Steel
Alloy steel contains additional elements such as chromium, nickel, and molybdenum, which enhance its strength and resistance to corrosion. This makes it suitable for more demanding applications.
Stainless Steel
Stainless steel offers excellent resistance to corrosion and high temperatures, making it ideal for chemical processing and other harsh environments. However, it is more expensive than carbon and alloy steel.